Decks
The two major factors in making a good skateboard is using good wood and good glue. Smaller factors such as the pressure the veneers are pressed at, and then the concave the veneers are pressed into. Check out some links to YouTube videos at the bottom of this page on board manufacture.
The Wood
The best decks are made of the North American Maple Hardwood. Of the 13 species of Maple found on the North American continent, 5 are used as lumber timber. 2 are of the "Hardwood" category and 3 are "Softwoods".The two Hardwoods are "Acer Saccharum" or "Sugar Maple" the other species is the "Acer Nigrum" or "Black Maple".
In Skateboard production only the "Acer Saccharum" or "Sugar Maple" is used. Other common names used for this species are, Sweet Maple, Thumb-nail Maple, Curly Maple, Birds Eye Maple, Hard Maple, Rock Maple. The term "Canadian Rock Maple" seems to have stuck in the skate industry as the name for this wood. But in reality, if you ask a North American logger what is the wood they make skateboards out of he'll tell you it's the SUGAR MAPLE.
Quote from the veneer mill; "You are correct. Sugar Maple is the only species used. Canadian Hard Rock Maple means nothing."
The Sugar Maple tree (Acer Saccharum) in its natural state.
So called Sugar Maple because of it's sweet sap. It is the main species used today for maple syrup production along with Black maple, though Sugar Maple is preferred and it's sap has twice the sugar content of other Maple species. The trees can grow to a height of 40 meters and live for up to 500 years old. It's wood is sort after for it's hard, heavy, strong and high impact resistant properties. It is commonly used for furniture, paneling, flooring and veneer, gunstocks, tool handles, plywood dies, cutting blocks, woodenware, novelty products, sporting goods, bowling alleys and pins, musical instruments... oh and skateboards.
Map showing distribution of "Acer Saccharum" in North America
The timber is logged in the north east regions of the USA and Canada. In particular the Great lakes and New England regions, extending into the south eastern regions of Canada like Quebec, Ontario and Nova Scotia. Trees have no borders. Veneer mills usually buy logs from all over these areas.
It is the Maple species itself, that makes this wood so good for skateboard production. It is strong and has a high resistance to impact. A common misconception is that the slow growth in these colder climates create a tighter growth structure and gives the timber is hard characteristics. In fact slow growth makes for a softer wood. It has been found that the replanted, new growth timber is faster growing and harder than the Old Growth forest timber.
Many cheaper skateboards are made from other species of Maple and also a similar looking wood to the Sugar Maple veneer a species of Birch, more commonly know in the skate industry as the "Chinese Maple".
Veneer Production
The next process is to turn a tree, or now log, into veneer ready to be pressed up into a skateboard. There are two basic and common ways that a log is turned into veneer. Slicing and rotary peeling.
Maple Logs ready to be peeled into veneer
Slicing is the method where a cutting blade is passed up the length of the log, slicing thin sheets off. The width of the sheet is only as wide as the log is. The Grain runs a different way to rotary peeled and it is a lot more flexible.
Rotary peeling is a method where the log is rotated around the ends, a cutting blade the length of the log is engaged and a continuous length of veneer is peeled off as the cutting blade is pushed into the log, as you would pull off a roll of toilet paper. The veneer from rotary peeling is much stiffer and it is this method that is used for veneer production for skateboards.
Maple veneer being peeled for skateboard production. Pictures courtesy of the two biggest skate veneer producers in the world both based in Wisconsin USA
The veneer strip is then cut into skateboard sized sheets. The sheets are then sorted into 3 different grades. Face sheets, Centre sheets and cross band sheets. The face sheets are usually sanded on one side. All the sheets are produced in a few different thickness', from 1.6mm, 1.4mm, to 1.2mm. Different combinations are chosen by the skate manufacturer to give the decks just the right thickness and strength.
The face and centre sheets have the grain running from nose to tail and the cross band sheets have the grain running from side to side. The face sheets are sorted out to have no knots or imperfections in them for looks, as they are the sheets that are seen. Some face sheets and centres are also dyed into the assortment of colours you see on and in your decks these days.
Natural Maple core or centre sheets in back and dyed face sheets front.
So a typical lay-up of a 7 ply skateboard goes like this. Face, centre, X-band, centre, X-band, centre, face.
The processed veneer is then cured to have an approx moisture content of between 6 - 8%. The logs are usually kept moist prior to peeling by constant watering by sprinklers or immersed in a tank to prevent end splitting by shrinkage and to help with obtaining a clean cut during the peeling process.
I have one more very important point I'd like to touch on as regards to deck strength. Wood is a natural product, and does vary greatly. Not only from tree to tree, but also from different sections of the same tree as the log is peeled down from sap wood to heart wood. It is hard to get consistency in strength & weight etc and it can not be controlled.
I'd like to include a quote from one major US supplier of Maple Veneer about tests conducted by a major USA manufacturer they supply.
Quote from the veneer mill, "I am not sure what technical information I can provide here given we are dealing with a natural product. I can tell you that through extensive testing by one of my customers regarding pop, rebound, bending strength and recovery, and shear testing they find as much as 50% variation from deck to deck. This means decks made with my veneer can have this much variation from the same veneer and there is the same amount of variance from his second supplier. He tested moisture of the veneer before pressing and that of the deck after pressing and cure time of 5 days and found no significant difference. So in the end the 2 factors he can not measure are the structural integrity of the wood in relation to density, modulus of elasticity and the quality of the cutting by the manufacturer".
So basically this means that all decks from the same manufacturer, and veneer supplier, using the same wood species, are not the same. Many manufacturers as mentioned above do get their veneer from a number of suppliers and a number of skateboard companies do get their boards from a number of manufacturers and in good faith are using the best veneer they can get to make your deck from.
That is why you may have one guy swearing by a particular brand and another guy saying he rode one and it snapped first day, or it lost it's pop really fast. It is this variation in wood that is generally the problem, not the veneer supplier, or the manufacturer using cheaper "Chinese Maple" or some other substitute wood. It is inherent in the natural make up of WOOD.
I have known this for many years. As you lay-up decks, you take one sheet after another from a stack of cores, you see the grain pattern slowly change, or the size/position of a small knot from sheet to sheet move, as they are stacked from the same peel/log. You can feel slight changes in weight and see the colour of the grains change etc as you go from sap wood to heart wood and back through the stack of veneers.
So please don't be too hard on a label if you get one dud. Most reputable companies are using 100%USA Hard Maple and the best glue and the best pressing techniques. It would most likely be just variations in the wood itself which can not be controlled, and not some conspiracy to make cheap dud products for profit.
Pressing
It is then that the skateboard manufacturer gets the veneer ready to be press into your favourite deck.
Veneer being coated with glue through the glue spreader
The veneer is passed through a glue spreader to coat the veneer sheets on both sides with glue. The glues used are usually a closely guarded secret, though there is only a few glue manufacturers that supply the majority of skateboard manufacturers. The type of glue could be best described as a crossed linked PVA. It is a water based glue and sets by the moisture being drawn out into the wood rather than a chemical catalyst hardening it. The type of glue used is the second major factor in the quality of a skateboard.
The coated veneers are laid up in the correct sequence, the stack (approx. 4 decks) is then placed into a hydraulic press with the particular concave moulds in between. As the veneers are pressed together, they slip against each other to form the concave and kicks etc, they are then left to harden and when pulled out they retain that form. I am constantly asked if they are steamed, NO they are not. The pressure at which they are pressed is the last major factor in the quality of a skateboard.
Two different types of presses. Left showing multi boards pressed in the one mould. Right showing single board press with multi moulds.
The veneer stack is left for only a short time in the press, as the glue sets very fast, in fact most manufacturers can recycle a set every 1 or 2 hours. The stack of blanks is then taken out and left to cure for a number of days. The blanks are cured so they can be cut out without clogging the cutting head. The blanks are very moist after they have been glued up and take a few days at least to dry out again and for the glue to set properly before machining. The best decks are cold cured, not heated to cure.
Stack of blanks left to cure for at least 3 to 5 days.
Machining
The steps of manufacture may vary from here on due to different machinery and techniques used by individual manufacturers.
The Moulds usually have small centre marking nipples on them to give the top blanks in the stack a small indent mark on one top side and on the top nose and tail to indicate the middle. The blank stack is then notched on the edge by a band saw at those indents to indicate on each blank below when separated the middle of the deck to position the cutting template and for drilling the holes, or the entire stack can be drilled in one hit, thus giving each individual blank it's positioning holes for the cutting out.
At this point the blanks are either cut out, then drilled, or drilled, then cut out, depending on the methods the manufacturers has set up for.
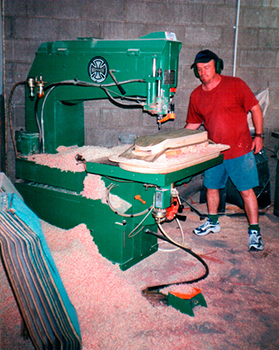
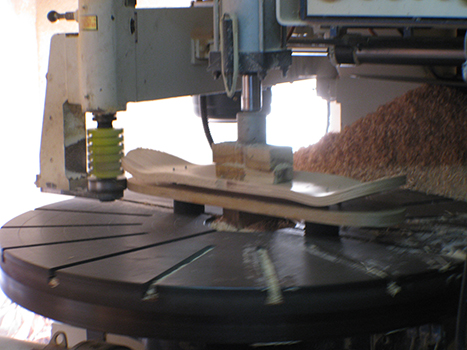
Left, Cutting out the blanks into the desired shape using an overhead router. Right, cutting decks out using a circular router.
Many different machines are used for this process, some use computer operated machines that can cut out 4 decks at a time. Some use template type overhead routers as shown above, and still many others use a hand cut table router. I prefer to use the hand cut method, it is rather fast and the cuts are cleaner, usually without chatter. The shape templates are vacuumed down, and the blank and template are then run around a cutting blade with a bearing on it that runs around the template shape.
Spindle sander to round and smooth the edges.
After being cut out the square edges of the deck are rounded off by running a trimmer router around the top and bottom edges to partially round the edges off before finishing off by hand sanding on a drum sander to round and smooth the edges.
4 head drill to drill the truck holes.
If the holes have not been done they are now. The deck is placed into a jig and the 4 holes are drilled in one hit. Bigger machines do the two sets of 4 in one go.
Coating and finishing
The decks are sprayed with a clear sealer coat.
The raw wood is now sealed with a clear sealer. When dry they are lightly sanded smooth, as when you apply a sealer the grain furs up and needs to be smoothed off.
It is at this point, depending on how the graphics are to be applied that the decks are either gloss coated or perhaps a base paint is applied ready for screen printing.
Screen printing the base of the decks direct.
The two basic ways of applying the graphics are either direct screen printing onto the deck, as above, the print may even be done on the face sheet flat, prior to lay-up. Or as below, printed onto a plastic film that has the graphic printed on it in reverse.
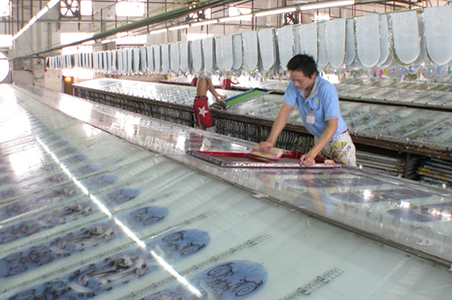
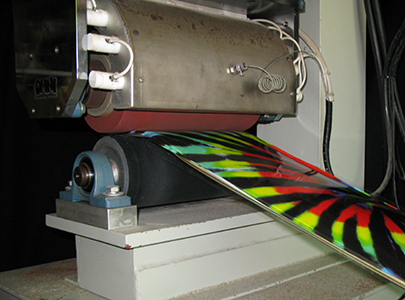
The "Heat Transfer" sheet is positioned onto the deck and then they are passed through a soft heated roller, the graphic sticks to the deck, the plastic film is peeled off, it is trimmed around, graphic done. The decks may be clear glossed after or usually left as is.
Finished glossed decks ready for sale.
The decks are then shrink wrapped and shipped out to the skate companies warehouse ready to then be shipped out to your local shop.
Decks ready for you to buy at your local shop.
You Tube link to board manufacture video